KIVO QMS
Quality Management for Medical Devices & Combination Products
A modern QMS designed for the unique regulatory needs of Class II & III medical devices, combination products, post-market surveillance, and more. Stay compliant, efficient, and audit-ready, at every stage of the product lifecycle.
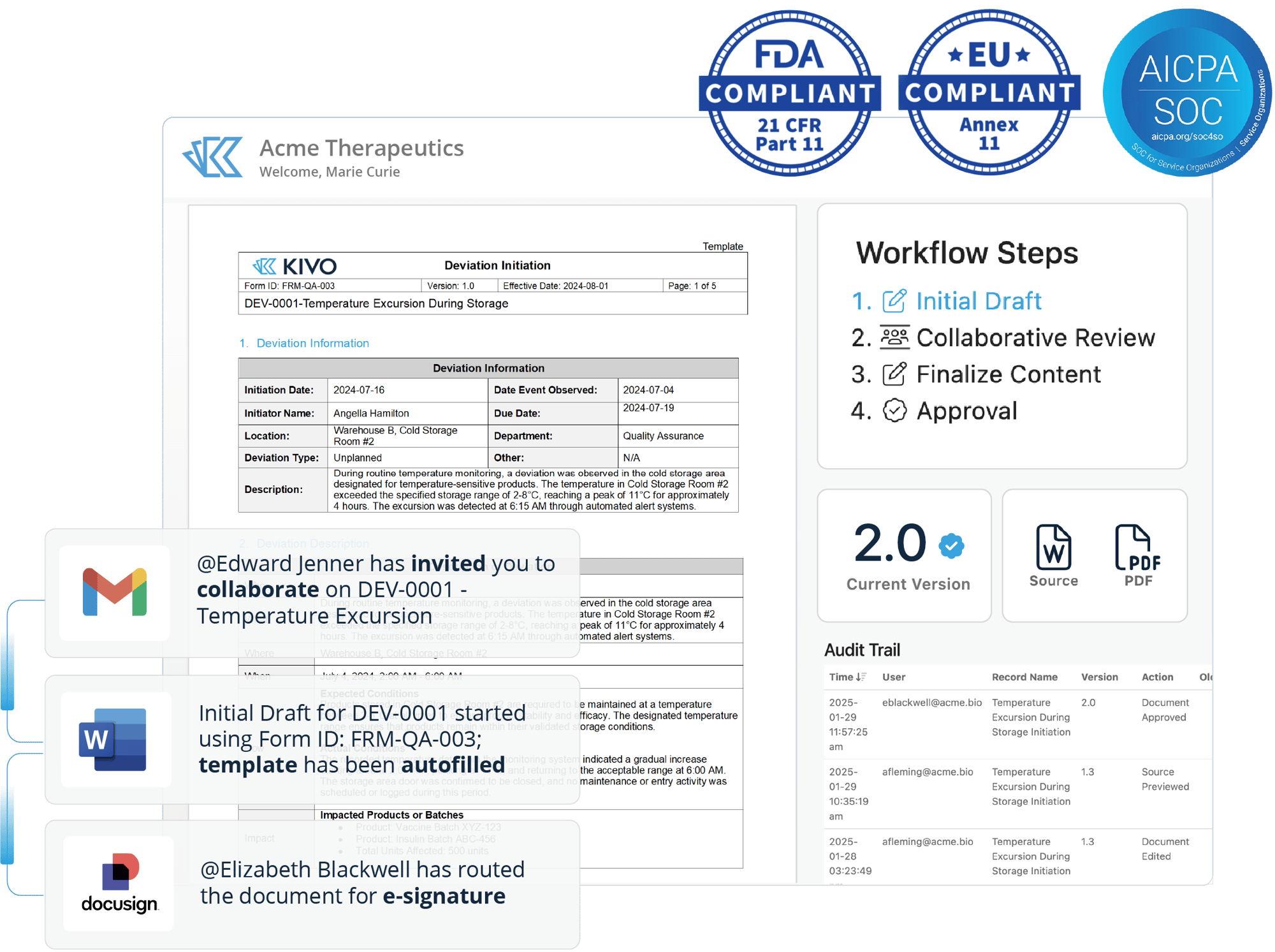
Fully Compliant, Less Complicated
Kivo’s fully validated, Part 11-compliant Quality Management System (QMS) helps you streamline every aspect of Quality operations without the complexity, cost, or delays of outdated legacy tools. Kivo QMS is designed for the unique needs of medical device and combination product development. We make it easy to control your DHFs, SOPs, CAPAs, change controls, audits, and so much more, in one intuitive, inspection-ready environment. Stay compliant, stay organized, and stay ahead of the competition with a QMS that is as agile as your team.
Confidently Manage Quality Events & Documents
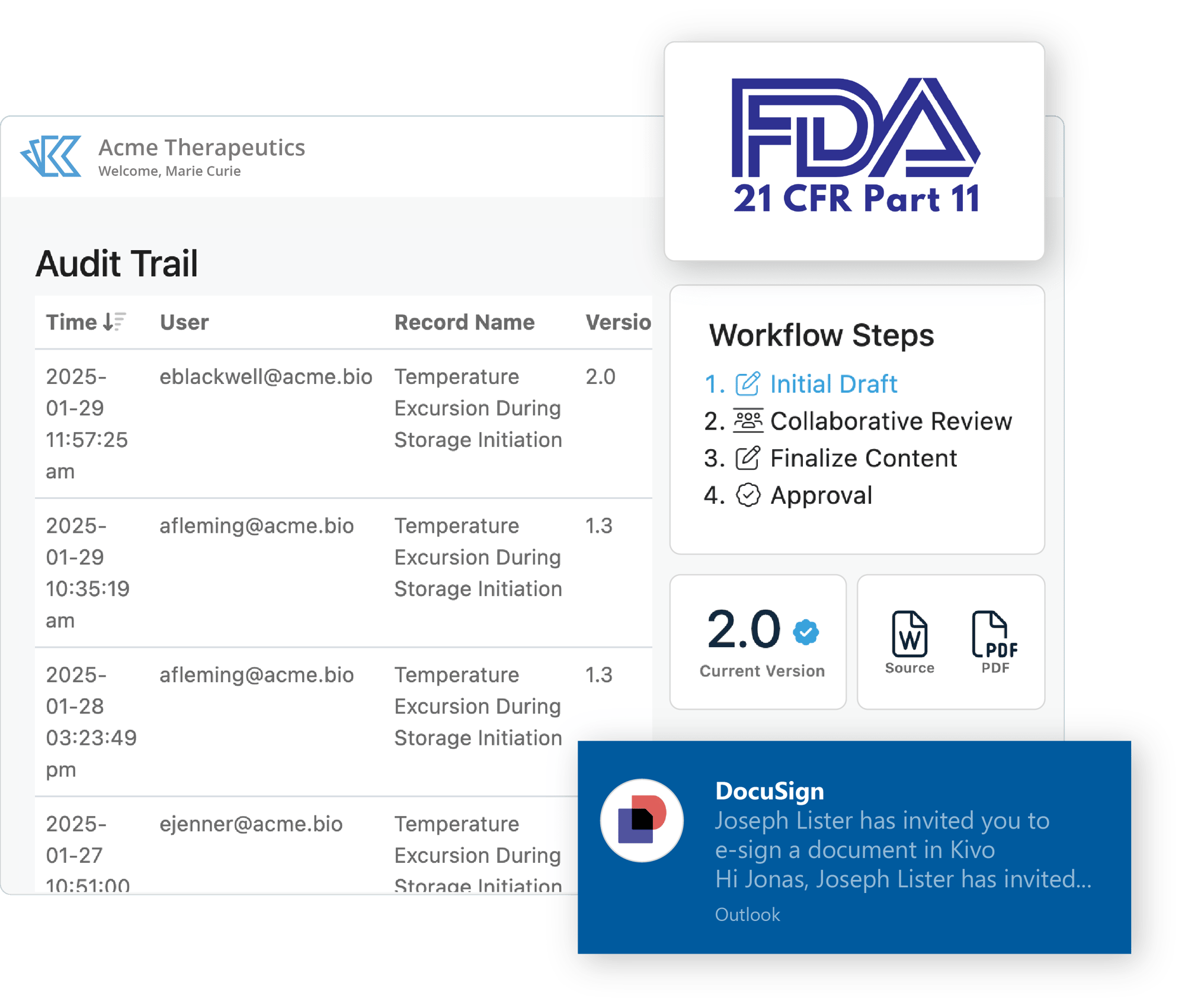
Controlled Documents
Kivo’s Quality Management System is built on our fully validated, Part 11-compliant Document Management Platform designed to meet the rigorous demands of medical device regulations like ISO 13485 and FDA 21 CFR Part 820.
- Role-based permissions to ensure only authorized users can create, edit, approve, or access key documents.
- Automated naming rules to maintain consistency across your device lifecycle documentation.
- Template-driven document creation to eliminate errors and speed up approvals.
- Customizable workflows for your design control, risk management, and post-market surveillance processes.
- Support for both audit-ready "simple approvals" and fully integrated DocuSign eSignatures, ensuring full Part 11 compliance every step of the way.
Quality and regulatory teams also rely on Kivo’s built-in Reporting and Dashboards to monitor document status, effective dates, review cycles, and upcoming renewals, giving you complete control over your document lifecycle.
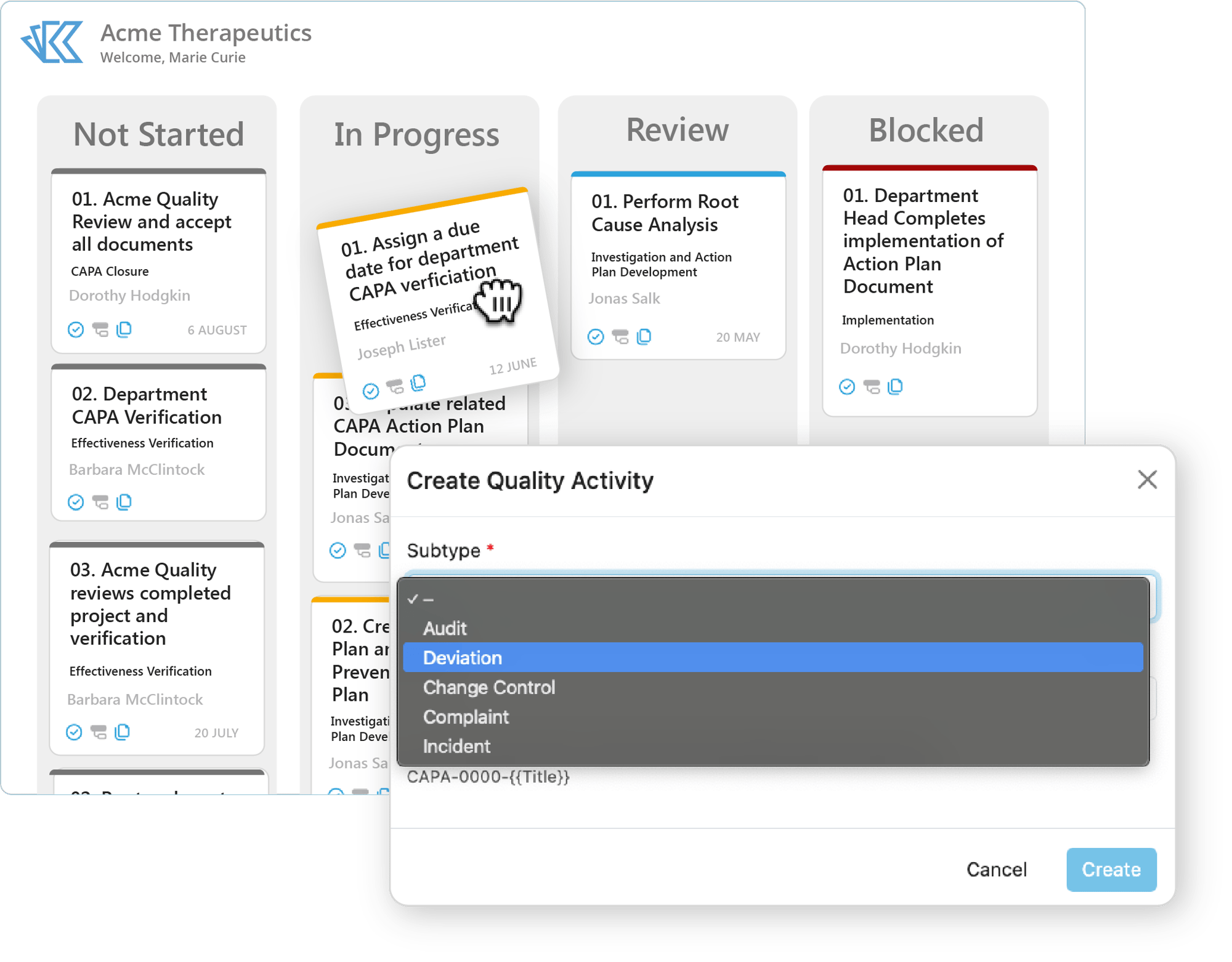
Quality Events
Kivo’s Quality Management System gives medical device teams a centralized, fully compliant platform to capture, manage, and track every type of quality event critical to maintaining ISO 13485 and FDA 21 CFR Part 820 compliance.
With configurable forms, device-specific templates, and automated workflows, Kivo helps you standardize and streamline how you manage:
- Incidents and product complaints
- Deviations and non-conformances
- Risk assessments and mitigation tracking
- Engineering change orders and change control activities
- CAPA (Corrective and Preventive Action) workflows
Every event type is fully customizable to align with your SOPs, regulatory expectations, and internal review & escalation processes. Kivo QMS also supports automated document creation from approved templates to save time and reduce errors.
Monitor progress in real time with custom dashboards, visual reports, and automated notifications, keeping your team on top of deadlines, corrective actions, and audit readiness at all times.

Audits
Kivo QMS empowers medical device teams to simplify, accelerate, and confidently manage audits across internal operations, suppliers, and partners, keeping you prepared for FDA inspections, Notified Body reviews, and customer audits alike. Key capabilities include:
- A dedicated ‘Inspector’ user role that enables secure, remote audit access for regulators, certifying bodies, and partners.
- A centralized Vendor Management hub with pre-built templates for audit planning, supplier evaluations, and documentation.
- The ability to easily link audits to related quality events like CAPAs, non-conformances, and risk assessments.
- Full audit trail visibility and access control to ensure all activities are tracked, documented, and inspection-ready.
With Kivo QMS, medical device companies can cut manual audit preparation time, reduce risk of findings, and stay ahead of regulatory and partner expectations without the stress of last-minute scrambles.
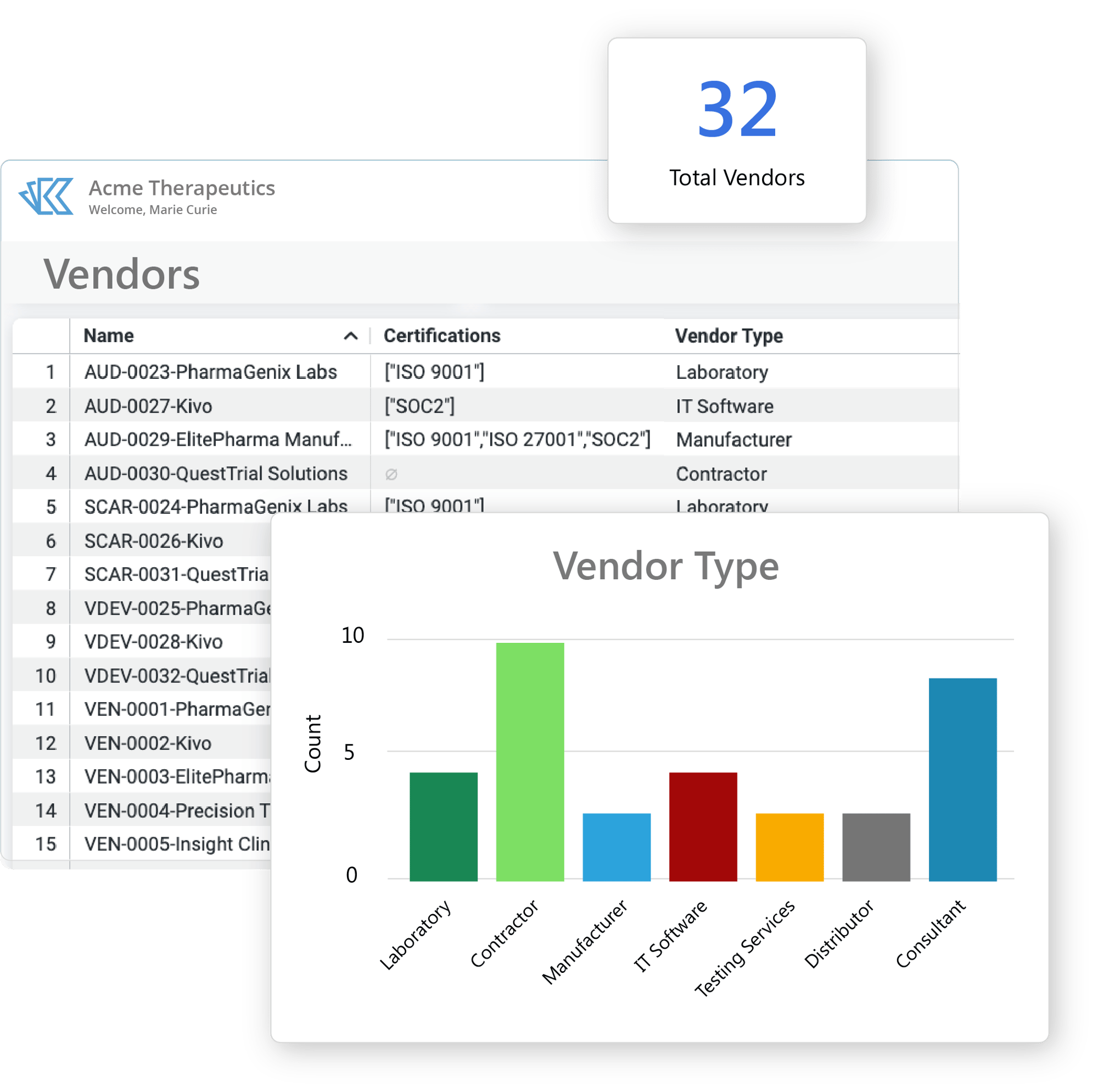
Vendor & Supplier Management
Kivo QMS provides medical device teams with a centralized, audit-ready platform to manage every aspect of vendor and supplier oversight, helping you meet the stringent expectations of FDA, ISO 13485, and global regulatory bodies.
- Create, manage, and store all vendor qualification documents, supplier questionnaires, and audit records in one secure, organized system.
- Track critical supplier data, including approval status, risk classifications, renewal dates, and performance trends.
- Plan and monitor supplier oversight activities with built-in project management and task tracking tools.
- Generate real-time dashboards and automated reports to maintain proactive oversight across your entire supplier network.
Kivo ensures that every supplier relationship is properly documented, monitored, and aligned with your compliance and quality standards, so your supply chain stays strong, transparent, and inspection-ready.
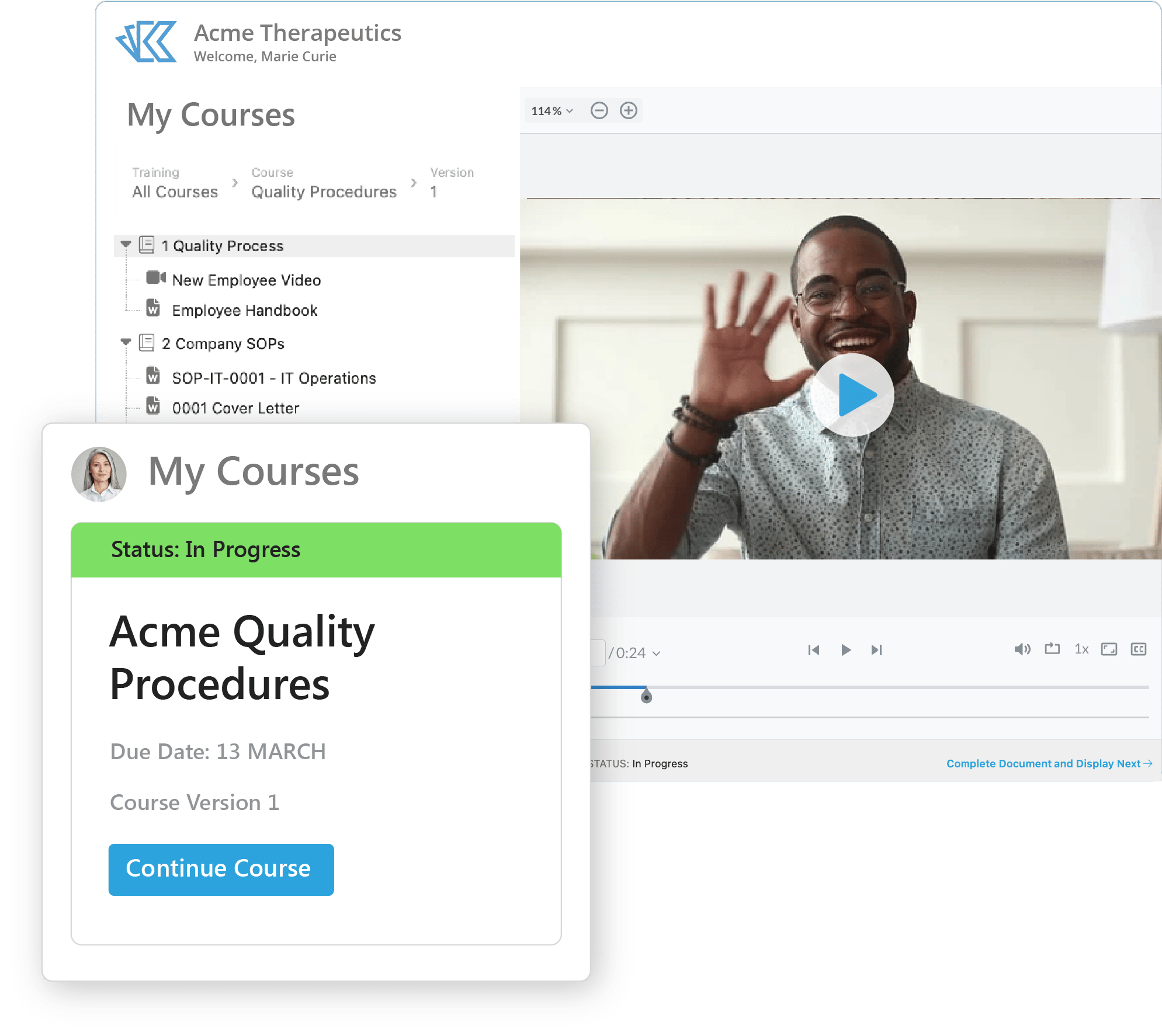
Training Management
Kivo QMS makes it easy for medical device companies to build, manage, and maintain a fully traceable training program, seamlessly integrated into your broader quality system and compliant with FDA and ISO 13485 requirements.
- Create training courses using SOPs, policies, videos, and presentations already stored in your QMS.
- Assign trainings by role, department, or individual, ensuring the right people are trained on the right procedures at the right time.
- Use our Training Reports to manage training compliance across employees, roles, and course elements.
- Link to external training content or upload external certificates and records to maintain centralized, audit-ready training documentation.
Kivo QMS makes training your team simple, scalable, and compliant, without the need for additional tools, complex integrations, or custom software development.
Security & Compliance Designed For Medical Devices
Kivo’s Quality Management System (QMS) is purpose-built for the unique regulatory requirements of the medical device industry, including combination product development, global compliance, and compliance with FDA 21 CFR Part 820, ISO 13485. From design controls to commercialization, our platform supports every stage of the product lifecycle with a modern, intuitive solution that enforces full compliance across your organization.
Kivo QMS enforces critical regulatory requirements around data integrity, traceability, electronic signatures, and security, ensuring that your documentation and processes stand up to FDA inspections, Notified Body audits, and partner due diligence. We even perform quarterly data integrity checks at no additional cost.
As a fully cloud-based QMS for medical devices, Kivo delivers pre-validated software updates, complete with validation documentation to simplify ongoing compliance and minimize disruption to your workflows.
Trusted by medical device manufacturers and combination product teams around the world, Kivo helps you stay compliant, connected, and confidently in control.
Visit our Trust Center to learn how we protect your data and uphold regulatory standards.
Features that scale. Costs that don't.
-
QMS FeaturesApproval Workflows with Part 11 Compliant E-SignaturesSmart Document PlaceholdersPre-Structured & Customizable Project TemplatesSecure Access and ViewingAuto-Associate Projects to Tasks, and Tasks to DocumentsIntelligent Reporting and Automated AlertsLink Trainings Directly to the DMS
-
General Kivo FeaturesAccess to eTMF, eCTD and RIM Included (No Integration Required)Role-Based, Per User Licensing for Full Platform, Limited Access, and 3rd-Party AccessDocument Linking with Aliasing (No Multi-Indexing Required)Seamless Integration with Microsoft Office OnlineCustomizable Metadata Across Features
-
IT & SecurityIntegrated CFR Part 11 Compliant eSignaturesNo IT Required (Fully Cloud Based)Single Sign OnFully Browser Based, Available for PC and Mac
-
SupportLightning Fast Support During Business Hours (Under 5 Minutes!)Unlimited Live TrainingImplement Within WeeksUnlimited Support
Dedicated Support from Day #1
Implement Within Weeks
Kivo’s pre-validated software and streamlined onboarding process make it easy for medical device teams to implement a fully compliant Quality Management System quickly and confidently. Our rigorous validation approach minimizes the burden on your internal resources. No drawn-out timelines. No unnecessary complexity. Expect fast, efficient, inspection-ready deployment in weeks, not months.
Unlimited Training
With Kivo QMS, you get unlimited training for your team: no limits, hidden fees, or dragged-out response times. Whether you're onboarding new employees, expanding into new markets, or adopting new features, our team is here to support you every step of the way, because we know having the best QMS is only powerful when your team can maximize its full potential.
Real Human Support
With Kivo, you get direct access to real human support: no frustrating chatbots, no endless ticket loops, and no long hold times. Our support team is available Monday through Friday, 6am–6pm PST, with average response times under 5 minutes. Our responsive, experienced support is one of the reasons medical device teams trust Kivo to keep their quality operations running smoothly.
Accelerate Quality Management
Get Kivo QMS today
Kivo QMS FAQs
1. What is a QMS for medical devices and why is it required?
A Quality Management System (QMS) for medical devices is a structured set of policies, procedures, and processes designed to ensure that products meet regulatory requirements and consistently achieve their intended performance. Regulatory bodies like the FDA and ISO require a formal QMS to protect patient safety, maintain product quality, and ensure traceability throughout the device lifecycle. Without a compliant QMS, companies risk delayed approvals, regulatory penalties, and costly recalls.
2. What regulations apply to quality management for medical devices?
Medical device companies must comply with several key regulations, including ISO 13485 (the international standard for medical device quality management) and FDA 21 CFR Part 820 (the Quality System Regulation or QSR for devices sold in the U.S.). Companies that market products globally may also need to meet additional requirements under the EU MDR (Medical Device Regulation) and MDSAP (Medical Device Single Audit Program). Kivo QMS is designed to align with all applicable regulatory frameworks and is also designed to handle the additional complexities of combination products.
3. How do I choose the best QMS software for a medical device company?
When choosing a QMS software for a medical device company, look for a system that is purpose-built for medical device compliance, not simply adapted from general industry standards. Key features should include support for design controls, risk management, document control, CAPAs, audits, training management, and supplier oversight. It’s also critical to select a platform that is Part 11 compliant for electronic records and signatures, offers validation documentation, and can scale as your company grows. Click here to see how Kivo QMS keeps you compliant at a fraction of the cost of legacy systems.
4. When should a medical device startup implement a QMS?
A medical device startup should ideally implement a QMS before beginning formal design and development activities (and typically before starting design controls). Establishing a compliant QMS early helps companies capture required documentation, manage risks, and avoid rework that could delay regulatory submissions like 510(k)s, PMAs, or CE markings. Waiting too long can lead to gaps that are costly and difficult to fix under the pressure of inspections or audits.
5. What features should a medical device QMS include?
A medical device QMS should include core capabilities such as document control, design history file (DHF) management, risk management, change control, CAPA tracking, nonconformance reporting, supplier management, training management, and audit readiness. Advanced QMS platforms also integrate dashboards and reporting tools to provide real-time visibility into compliance activities. For combination products, it’s important that the QMS can support both device and pharma requirements seamlessly. Kivo QMS is a modern solution built to handle these exact needs while providing an easy, intuitive user experience and costing a fraction of the price of legacy systems.
6. How does a QMS help with FDA inspections and ISO audits for medical devices?
A well-structured QMS helps medical device companies stay inspection-ready by ensuring all required records, approvals, and traceability are in place and easily accessible. During an FDA inspection or ISO audit, regulators will review your procedures, training records, design documentation, risk assessments, and CAPA processes. A compliant QMS like Kivo simplifies this process, reducing the risk of findings, warning letters, or certification delays, and helping demonstrate a strong culture of quality to regulators.
7. What are the benefits of using a cloud-based QMS for medical device companies?
For medical device companies, a cloud-based QMS can significantly accelerate inspection readiness, streamline supplier and training oversight, and support faster product development cycles. Cloud-based systems also offer faster implementation, lower upfront costs, and easier scalability as your business grows. Unlike on-premise systems, cloud systems provide real-time access to quality data from anywhere, enabling cross-functional teams to collaborate seamlessly across locations. They also reduce the burden of maintaining validation and security internally, as reputable vendors deliver pre-validated updates and handle infrastructure compliance.
8. How does a QMS handle CAPAs, deviations, and audit trails?
Kivo QMS provides structured workflows to manage CAPAs (Corrective and Preventive Actions), deviations, and audit trails in a compliant, traceable way. When a deviation or nonconformance is reported, the QMS routes it through predefined steps for investigation, root cause analysis, corrective action planning, and effectiveness checks. CAPAs can be linked directly to related deviations, audit findings, or risk assessments, creating a fully traceable chain of quality events.
Kivo QMS also automatically maintains a detailed audit trail that records every action, edit, approval, and timestamp throughout the process, ensuring full transparency and compliance with FDA 21 CFR Part 820, ISO 13485, and other regulatory standards.
9. Can a medical device QMS handle both design controls and post-market surveillance?
Yes, Kivo QMS handles the entire product lifecycle, from initial design controls through post-market surveillance activities. This includes capturing user needs, design inputs, verification/validation records, and ongoing data from complaints, adverse events, and field actions. Having all phases connected within a single QMS helps ensure traceability, accelerates audits, and supports continuous product improvement after market launch.
10. How long does it take to implement a QMS for a medical device company?
While most QMS providers promise timely implementation, the most popular legacy systems usually take 3-6 months to rollout, and that doesn't even include the lengthy training needed to get teams up to speed. By contrast, Kivo offers a modern, pre-validated QMS platform that can be deployed in just a few weeks. Our solution is 1/10th the cost, incredibly easy for your entire team to learn, designed specifically for medical devices and combination products, and able to be fully operational within the next few weeks. Enter your info below to see Kivo QMS in action and learn why so many life sciences teams are switching to our system.
Accelerate Quality Management
Get Kivo QMS today